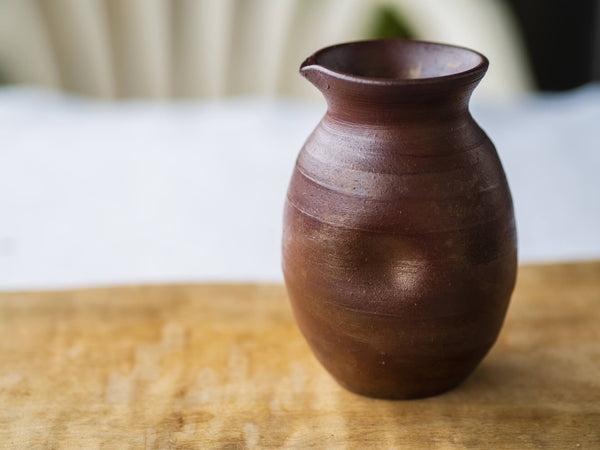
Bizen Pottery: A Timeless Tradition of Unbreakable Elegance
Bizen Pottery is designated as a traditional Japanese craft. What kind of ceramics is Bizen Pottery, which was recognized as a Japanese Heritage in 2017? We will introduce Bizen Pottery, including its charms.
What is Bizen Pottery?
Bizen Pottery is a ceramic ware produced in Bizen City, located about two hours by car from Osaka. It has a very long history among the many types of ceramics in Japan.
Pottery with a History of 1,000 Years
It is said that the production of ceramics began around the Heian period (794-1192) and has a history of 1,000 years. The pottery is formed one piece at a time with high-quality clay, dried, and fired without painting or glaze, and is characterized by the well-defined clay flavor. The unique patterns of Bizen ware are created by the way the pieces are packed in the kiln and the way the pine split wood used as fuel is burned. Bizen ware is a hard pottery that is slowly fired over a period of 7 to 10 days by the power of a flame at more than 1,000 degrees.
Bizen Pottery is One of the Six Ancient Kilns of Japan
Nihon Rokkoyo is the collective name for six representative kilns (Seto, Tokoname, Echizen, Shigaraki, Tanba, and Bizen) that have been in production since the Middle Ages (late Heian Period to Azuchi-Momoyama Period). Japan boasts a long history, and while various kilns have been created over the years, many kilns have bankrupted. In the midst of this, the antique ceramics researcher Fujio Koyama investigated the history of Japanese kilns and found that the above-mentioned six kilns have been in continuous production from ancient times to the present. They were named the "Six Ancient Kilns" of Japan" by him, and were recognized as "Japanese Heritage" in 2017.
History of Bizen Pottery
There are five main phases in the history of Bizen ware.
(1) Kofun Period: The Roots of Bizen Pottery
Bizen Pottery is said to have its origins in the gradual change of the Sue ware production method during the Kofun period, when bowls, plates, and roof tiles for livingware were produced during the Heian period (794-1185). At this time, the reddish-brown color characteristic of Bizen ware was still absent, and Sue ware was characterized by its white and gray color. Sue ware was characterized by being harder and harder to break than the earthenware (Hajiki) produced during this period, and gradually spread among the general populace.
(2) Kamakura Period: The prototype for today's Bizen ware was created.
During the Kamakura period, jars, pots, and mortars were mainly made, and gradually the reddish-brown surface characteristic of today's Bizen ware began to be produced. It has been confirmed that kilns gradually became larger and larger from this period, with kiln sizes increasing from around 10 m to 20 m and 30 m.
(3) Muromachi Period: Efficient production became possible
In the Muromachi period, mass production of Bizen ware became possible. The use of rocro began to be used for forming vessels, and efficient production was achieved by firing in large kilns, which spread over a wide area. In the late Muromachi period (1333-1573), the simplicity of Bizen ware was recognized by Juko Murata as being in harmony with the wabi-sabi of the tea ceremony, and its appeal as tea ceremony pottery was enhanced.
(4) Edo Period: Mass Production by Large Kilns
In the Edo period (1603-1867), small kilns were integrated under the protection of the feudal domain, and large kilns were used for mass production. These integrated large kilns were called Kyodo Kilns, and production of Bizen ware was controlled by the six surnames of the kiln owners (Kimura, Mori, Tongu, Terami, Oyoshi, and Kaneshige). On the other hand, the types of Bizen ware produced after the Muromachi period (1333-1573) included tea utensils and daily utensils, as well as figurines. While production at these large kilns continued until the end of the Edo period, the production of porcelain began to flourish in Kyoto, Arita, Seto, and other areas, and Bizen ware gradually began to decline.
(5) Meiji Period to the Present: Spinning the fire through the difficult times to the present day
As the production of porcelain became more active, Bizen Pottery continued its efforts to keep the kiln fires burning by making not only tokkuri (sake cups) and sake cups for daily use, but also bricks and clay pipes. During the war, Japan was short of metal, and Bizen ware, which boasted high hardness, was even used to make hand grenades. According to surviving documents, 40,000 units were ordered from the kiln, but the war ended before any Bizen ware grenades were actually used.
Bizen Pottery shows various faces as time goes by. It was Living National Treasure Tōyo Kaneshige who led Bizen-yaki from this decline to its current prosperity. In 1956, Tōyō Kaneshige was designated by the national government as a holder of Important Intangible Cultural Property (Living National Treasure), which triggered the efforts of many people and brought Bizen out of its period of stagnation. This led to a period of stagnation, which was followed by the efforts of many people, and the popularity of purely Japanese Bizen ware increased not only in Japan but also abroad. Today, artists and potters continue to produce unique pieces in addition to traditional styles, one by one.
Characteristics of Bizen Pottery

Bizen Pottery is so hardy that it is said to be "unbreakable even when dropped," and is characterized by its ultimate simplicity: no glaze is used and no painting is done. In the past, jars, mortars, and large turtles were made of Bizen ware, and today they are mainly used as teapots, mortars, plates, teacups, and vases. While firing at high temperatures of 1200-1300 degrees Celsius, patterns are created by the properties of the clay, the way the kiln is filled, temperature changes, and the influence of ash and charcoal during firing. Bizen Pottery's appeal lies in its depth of flavor, with no two pieces having the same color or pattern. It can be said that the more you use Bizen Pottery, the more it becomes more attractive. Bizen ware is also useful as a beer glass because of its fine pores and the fine bubbles that form due to the unevenness of the pores. Bizen ware is popular for making ordinary beer taste better just by drinking it out of a Bizen ware glass.
Seven types of "Kiln Transformation," the charm of Bizen Pottery
The patterns that are the charm of Bizen ware are brought about by "kiln alteration" during firing. Kiln alteration refers to the changes that occur in a vessel during firing. The firing color and pattern change depending on the position of the pot in the kiln and the firing conditions. Here are seven typical kiln changes.
Sesame(Goma)

The name "sesame" is derived from the fact that the ash from the split pine wood used to fire the kiln adheres to the piece, giving it the appearance of being sprinkled with sesame seeds. In modern times, the work is sometimes fired with the ashes dipped in it beforehand, as if it were intentionally sprinkled with sesame seeds. Various colors and patterns are available, including white and yellow.
Sangiri

When a work on the kiln floor is buried in ash, it is not directly exposed to the fire and air flow is reduced, resulting in kiln deformation. The area directly exposed to the flame turns reddish brown, the area buried in ash turns black, and the border between the flame and the clay turns gray or blue.
Botan-mochi

A small piece of clay is placed on a plate, bowl, etc. and fired. The unevenly burned areas are round and look like peony cakes, hence the name "botan mochi. The color of the peony rice cake varies from the center, which is in direct contact with the fire, to the periphery, which is slightly exposed to the fire, and can be red, brown or white.
Hidasuki

Hidasuki is called "Hidasuki" because it looks like a bright red (scarlet) colored tasuki. This pattern is made of rice straw. Originally, straw was wrapped around the pieces to prevent them from sticking to each other when they were packed in the kiln, and it is now used as a pattern. The pattern of red, brown, and vermilion lines on a light-brown background, which are arranged like a "tasuki" (a sash), is even more atmospheric.
Kurobizen(Black Bizen)

Kurobizen is one of the Bizen ware produced in the Kobizen period of the Edo period, and only a few pieces from that period remain. The black color of Kurobizen appears when the piece is coated with muddy clay containing high iron content and fired. The iron-rich clay quickly dissolves into the clay on the surface of the vessel during firing, and the vessel becomes shiso to black in color. The color intensity of the finished product varies depending on the iron content of the clay on which the surface coating is applied.
Aobizen(Blue Bizen)

Aobizen is fired in a kiln where the kiln has a strong oxygen-removing (reducing) effect. Bizen clay contains high iron content, which gives the pieces a blue-gray to black color. There are only a few places in the kiln where the kiln can be in a reducing state, and the colors do not always turn out as intended.
Shirobizen(White Bizen)

Shirobizen is made from white clay with a white or transparent glaze and fired at high temperatures. The process of making Shirobizen varies from artist to artist, but it is said that by firing clay with low iron content, it became possible to produce white without using glaze.