
Japanese Ceramics:Perfect Guide to 20 Types of Pottery and Porcelain
What is the Difference between Pottery and Porcelain?

The main differences between pottery and porcelain are raw materials, texture, hardness, water absorbency, and firing temperature. There are four major differences between pottery and porcelain.
Raw materials: Pottery is made mainly of clay, while porcelain is made mainly of stone.
The main raw material for pottery is clay, while the main raw material for porcelain is stones such as kaolinite, silica stone, and feldspar.Clay used for pottery has coarse particles and many fine pits. Therefore, the surface of porcelain has a rough texture when fired, whereas the raw materials used for porcelain have very fine particles and are smooth to the touch.This difference in raw materials also results in a difference in water absorption. Pottery has countless fine holes, so its water absorption rate is approximately 10%, while porcelain's is almost 0%.

While these microscopic holes in pottery give it a different texture and flavor as a vessel, they also make it easier for the color and smell of food to stick to it. To prevent this, the vessel is soaked in a starchy liquid such as rice water or flour to coat it, which is called "medome"(seasoning).
Firing temperature: low for pottery, high for porcelain

Pottery is fired at 900~1,300 degrees Celsius and porcelain at around 1,200~1,400 degrees Celsius.This difference is caused by the difference in temperature at which the raw materials, clay and stone, dissolve. Glaze is applied to pottery to make the surface shiny, and is baked at the above temperatures because it melts at around 900 to 1,300 degrees Celsius. Feldspar and silica, the raw materials of porcelain, melt at temperatures as high as 1,200 to 1,400 degrees Celsius and change into a glassy substance. The glassy texture of the changed glassy material gives porcelain its characteristic slippery feel, and since it fills the space between the particles, it does not absorb water.
Period when it was first made: 1,000 years for pottery, 400 years for porcelain in Japan

The origin of pottery dates back more than 10,000 years. Pottery made from clay has been found throughout Japan, and its full-fledged history began around the Heian period. In the Kamakura period (1192-1333), various kilns were built throughout Japan, and the venerable kilns known as the Six Ancient Kilns of Japan (Rokkoyo) were established.Porcelain began to be produced in the Edo period, so its history is relatively short compared to pottery. The history of porcelain production began when potters from Korea came to Japan and discovered the raw materials for porcelain in Arita Town, Saga Prefecture. Porcelain production techniques were developed on the Korean peninsula, and as these techniques spread to Japan, they have been handed down to the present day. Although the supply-demand structure of pottery and porcelain has changed drastically with the passage of time and the historical background, both products are currently favored by many people.
Texture to the touch: Pottery is rough and porcelain is smooth


The surface of pottery is porous and rough to the touch. Porous means that there are invisible holes everywhere, and when you touch it with your hand, you feel the rough texture due to the unevenness of the surface.These microscopic holes on the surface allow the drink to be covered with bubbles, making it more palatable and tastier. (Beer tastes better because it retains its foam, and tea tastes deeper and mellower!) ) Another charm of pottery is that you can develop your own original vessels, as the patterns and textures change as the vessel absorbs liquid.
Porcelain, on the other hand, has a dense and slippery texture. Porcelain clay, the raw material of porcelain, becomes smooth like glass when it is fired. Porcelain is sometimes used as tableware, but another charm of porcelain is that its smooth surface can be decorated with beautiful paintings and enjoyed as an object of appreciation. It can be used as tableware and daily utensils, and its high value as a work of art is a characteristic of Japanese porcelain.
Usage Scenes of Pottery and Porcelain

Serving side dishes in a teacup or plate, or drinking sake in a tokuri (Japanese sake cup) with a choko (chopstick) will make ordinary dishes taste even better. By paying attention to the dishes that decorate them, you can add variety to your dining table. Pottery can also be used as interior decorations, vases, flower arrangements, etc., to make our daily lives more colorful and relaxing. In our busy and stressful modern society, a calm space is mentally healing and a relaxing space is very valuable. Japanese pottery and porcelain can be used for a wide range of purposes, from everyday items such as tableware and daily utensils to interior decorations.
Methods and precautions for ceramic care
Pottery and porcelain have handling methods and precautions depending on the product.The table above is general information, but details vary from product to product, so please refer to the instructions that come with the product if available. The usage period and durability of vessels vary depending on how they are used and cared for. We will show you how to carefully care for and nurture your vessels.
Be careful of sudden temperature changes and microwaves

Basically, both ceramic and porcelain vessels can be used in microwave ovens. Some pottery can be heated by putting them in a microwave oven with liquid, and some products are labeled as usable. However, since pottery are highly absorbent and contain a lot of water, the base of the ware itself can easily become hot, and in the worst case scenario, the ware may crack. In some cases, the microwave oven may work fine for a few times, but repeated use may result in cracks. When using pottery in a microwave oven, please check the instructions that come with the product thoroughly. If there are no instructions, it is safer not to use the microwave oven.
On the other hand, porcelain has almost 0% water absorption, so there is little risk of cracking even when heated to high temperatures. Basically, using a microwave oven is not a problem. However, porcelain with gold or silver decoration should not be used in a microwave oven. This is because the electromagnetic waves of the microwave oven reflect off the gold and silver. This is also stated in the instruction manual, so we recommend checking this before use!
How to wash and care for pottery

After you have finished using the pottery, wash it with a soft sponge and dishwashing detergent.The key is to dry it thoroughly after washing. When using a dishwasher, be careful that the water pressure does not cause the vessel to shake. The rim of the bowl is made especially thin, so it tends to chip easily. If the vessel has a design with a picture on it, the water pressure may cause the picture to fall off, so it is best to wash the vessel gently by hand.
There are two washing methods that should not be done.The first is to "leave it soaking for a long time". Pottery is highly water absorbent, so if you leave it soaking for a long time, the base will absorb dirt. This can cause mold and stains, so it is recommended to avoid soaking the pots for a long time and wash them quickly. The second is to use "hard sponges, gold scrubbers, and cleansers". Washing with hard objects may scratch the surface and cause damage when using a microwave oven. Please wash them with a soft sponge.
11 Famous Japanese Porcelain
There are 11 types of representative porcelain in Japan.We will introduce them in detail, including famous porcelains such as Arita porcelain, Hasami porcelain, and Kutani porcelain!
Arita/Imari Porcelain

Arita/Imari porcelain is porcelain produced in Arita Town and Imari City, Saga Prefecture. It is the "father of Japanese porcelain" and has had a great influence on the history of porcelain in Japan.Arita/Imari porcelain has beautiful patterns and designs, and is used in a wide range of products from utilitarian items such as plates, bowls, and vases to items with high artistic value such as decorative objects and antiques. Production began in the Edo period (1603-1867) and developed as the oil kiln of the Nabeshima clan that ruled Imari and Arita at that time.
Did you know that Arita/Imari porcelain, which is produced using advanced techniques, is exported not only to Japan but also to other countries, and has influenced Meissen porcelain in Germany? Arita-Imari porcelain is a representative of Japanese porcelain, loved by royalty and aristocracy, and has a high antique value.
Hasami Porcelain

Hasami porcelain is porcelain fired in Hasami-cho, Nagasaki Prefecture. The beauty of its translucent white porcelain and the delicate patterns painted with gosu (a type of porcelain) fascinate those who use it. Openwork and braided patterns are the techniques used to enhance the elegance of Hasami-ware.
Such Hasami-ware originated about 400 years ago, when porcelain production began in Japan. Porcelain production began in the neighboring town of Arita, which in turn was passed on to Hasami-cho, opening the door to porcelain production. Hasami porcelain, which was born as a common people's vessel, has cultivated a wonderful traditional beauty throughout its long history.
Kutani Porcelain

Kutani yaki is porcelain made in the area around Kaga City, Ishikawa Prefecture. Kutani porcelain is characterized by its vivid colors, bold and graceful patterns, and the use of a technique known as kami-e-tsuke (overglaze painting).Both porcelain and ceramics are produced in Kutani porcelain, but the clear name "Kutani porcelain" refers to overglaze enameling done in Kutani.Ue-etching is a technique of painting with pigments on top of the glaze and re-firing.The pigments used for overglaze painting can be fired at about 800 degrees Celsius, so there are fewer restrictions on the pigments, and a wide variety of colors can be enjoyed. Kutani porcelain produced with this variety of colors is highly popular as beautiful vessels.
Tobe Porcelain

Tobe ware is produced in Tobe Town, Ehime Prefecture. Tobe is said to be the best pottery village in Shikoku, and production began about 250 years ago. Tobe ware has a beautiful white porcelain surface with blue underglaze blue, and is used as tableware, flower vases, cups, and other practical everyday utensils. It is sturdier and heavier than porcelain from other kilns. Its thick, chunky form is also characteristic, and it is highly valued for daily use because it is resistant to cracking and chipping. The fact that the tradition of handmade and handwritten work is maintained is another point that is highly valued.
Incidentally, one of the characteristics of Tobe ware is its "durability. It is so strong that it is also called "fighting ware" because it is said that it does not break even when thrown at a couple in a quarrel. Please note that we do not recommend throwing the tableware in a quarrel between husband and wife.
Seto Porcelain

Seto porcelain is the general term for pottery produced in Seto City, Aichi Prefecture. Due to Seto's historical background, both pottery and porcelain are currently produced. Incidentally, Seto porcelain is so well recognized as pottery in Japan that it is called "Setomono" as a synonym for pottery. Such Seto ware is counted as one of the "Six Ancient Kilns of Japan," the six types of pottery with the longest history in Japan, and one of the "Three Great Ceramic Wares of Japan. The clay from Seto is characterized by its low iron content, which allows for a white finish when fired, making Seto porcelain pottery look good with a wide variety of glaze colors.
Mino Porcelain

Mino ware is one of Japan's representative ceramics. Its beauty and diversity have made it very familiar, accounting for half of the domestic market share in Japan. Produced in Gifu Prefecture, formerly known as Mino Province, located in the central part of Japan's main island of Honshu, Mino ware boasts a long history and has been produced in a variety of colors and shapes over the years. Mino ware is characterized by its diversity; more than 15 different styles have been developed to date, and the techniques have spread beyond a single form. Mino potteries are scattered throughout eastern Gifu Prefecture, with Tajimi, Toki, Mizunami, and Kawagoe cities being the main centers of Mino pottery production.
Kyo and Kiyomizu Porcelain

Kyo and Kiyomizu porcelain are Kyoto's representative traditional crafts. In the lands where the capital was located in the past, a variety of technicians, techniques, and cultures mingled to create unique pottery. In fact, "Kyo porcelain and Kiyomizu porcelain" do not have a specific style or technique, but are characterized by a combination of diverse styles and techniques from all over Japan. This is thought to be due to the fact that Kyoto was a place where materials and craftsmen gathered from all over Japan, and the environment in which culture flourished under the patronage of temples and shrines, the imperial family, and aristocrats. Today, Kiyomizu porcelain and Kyo porcelain ceramics are still produced entirely by hand, and Kiyomizu porcelain and Kyo porcelain ceramics today are fired with the polished skills of artisans. It is also a rare area where delicate painting, graceful forms, and new techniques of each era are fused together.
Mikawachi Porcelain
Mikawachi Porcelain is porcelain fired in the area around Sasebo City, Nagasaki Prefecture. Originally made as an official kiln to present porcelain to the Hirado clan during the Edo period, it was sold as delicately crafted vessels to wealthy people in Japan and abroad after the abolition of the han system. The patterns on Mikawachi ware are all hand-painted, a technique that has been handed down to the present day.
Amakusa Porcelain

Amakusa porcelain is made in the Amakusa region of Kumamoto Prefecture. Amakusa has been producing pottery and porcelain since ancient times due to the abundance of high quality pottery stones. The production of ceramics and porcelain dates back to around 1650. At that time, the production and distribution of porcelain for common people spread, as it was not presented to the feudal lords. The characteristic of Amakusa porcelain is its "clear white color. The high quality of the pottery stone is deeply connected to the production of beautiful porcelain, and the whiteness of the porcelain seems to be absorbed into the body just by looking at it.
Izushi Porcelain
Izushi porcelain is porcelain made in Izushi Town, Hyogo Prefecture. Its history began with the opening of a kiln in 1784 in Izushi Town, and full-scale production began in 1799 with the discovery of pottery stones in the town. Initially, production was conducted under the protection of the Izushi clan, but gradually private kilns began to produce more and more porcelain, and the town flourished. Porcelain fired in Izushi is characterized by its clear and unique white color. It is not a blue or warm white. This unique whiteness is achieved by the raw material, Kakitani pottery stone.
Aizu Hongo Porcelain
Aizu Hongo porcelain is a traditional craft produced in the Aizu region of Fukushima Prefecture. Both ceramics and porcelain are produced, and the porcelain is often beautifully painted with Gosu (a type of pigment used in dyeing) and Japanese and Western paints. The porcelain production of such Aizu Hongo ware was brought about by Ihei Sato. Around 1800, when the history of porcelain production began in Aizu, Ihei Sato infiltrated Arita, a pioneer in porcelain production, and risked his life to learn the technique. After returning to his clan, Ihei Sato opened a kiln and expanded production under the protection of the clan, and as time went by, private craftsmen also began to produce.
9 Famous Japanese Pottery
So far, we have introduced pottery. However, the word "pottery" is not a simple word, and the traditions, history, and techniques of Japanese pottery are quite different depending on the region where they are produced! In this article, we will introduce 9 representative types of pottery in Japan.
Mashiko Pottery

Mashiko Pottery is produced in Mashiko Town, Tochigi Prefecture.
The clay from Mashiko contains many air bubbles, which makes it unsuitable for fine work, and the thick, chunky forms are characteristic of this type of pottery. Mashiko ware sold so well during the Meiji period (1868-1912) that the number of suppliers increased and poor quality ware began to appear on the market. However, as the times changed, the demand for pottery declined and the market went into a slump. The company temporarily discontinued production, but after the Great Kanto Earthquake of 1923, demand for kitchenware rapidly increased. The pottery has repeatedly prospered and declined, and has continued to the present day.
Hagi Pottery

Hagi ware is produced in Hagi City, Yamaguchi Prefecture in western Japan.
In the world of the tea ceremony, it is so highly regarded by tea masters that it is called "Ichiraku, Ni-hagi, San-karatsu. Various patterns are produced depending on the clay mixture, glaze application, and firing in a climbing kiln. Hagiyaki has a characteristic called "Nanakake," in which tea or sake permeates through cracks on the surface of the vessel after many years of use, gradually changing its appearance. Hagi ware is characterized by the fact that this change is seen as beauty and gives a sense of apology and sabi.
Bizen Pottery

Bizen Pottery is produced in Bizen City, Okayama Prefecture.
It has a history so old that it has been selected as one of the Six Ancient Kilns in Japan, and has been in production for 1,000 years. Bizen Pottery is fired one by one at a high temperature of over 1,000 degrees Celsius for 7 to 10 days, and is said to be so hard that it will not crack even if dropped. Bizen Pottery is characterized by changes in the kiln depending on the way the kiln is filled. There are seven different types of Bizen ware, and if you would like to know more about them, please refer to the following article.
Satsuma Pottery

Satsuma pottery is a type of pottery produced in Kagoshima Prefecture.
It can be classified into two major types, Kuro-satsuma and Shiro-satsuma, and each has developed differently. Shiro-satsuma was produced under the protection of the clan, and was mainly used as an offering and for ornamental purposes. On the other hand, Kuro-satsuma was made for daily use by common people, such as kyusu (teapot), tokkuri (sake cup), and earthenware bottles.
Karatsu Pottery


Karatsu ware is produced in Karatsu City, Saga Prefecture, in the Kyushu region.
Like Hagi ware, Karatsu ware is also highly regarded as a tea ceremony utensil by tea masters, who say "Ichiraku, Ni-hagi, Sangaratsu" (one for Raku, two for Hagi, and three for Karatsu). It is a must-know pottery for those who enjoy the tea ceremony. Karatsu ware has different faces depending on the technique, such as Eko-karatsu, Chosun-karatsu, and Motto-karatsu. The tapping technique handed down from ancient times also brings out a rustic flavor and gives a deep sense of wabi-sabi.
Tokoname Pottery

Tokoname ware is pottery produced in Tokoname City, Aichi Prefecture. It belongs to the Chita Peninsula, and the pottery clay from this region is characterized by its high iron content, which gives it a reddish-brown color when fired. The teapot used for making tea is especially famous. When tea is brewed in a Tokoname ware teapot, the iron content is dissolved, and the bitter taste of the tea is mellowed and deepened. Tokoname-yaki is recommended as an everyday ceramic ware.
Tamba Pottery

Tamba-yaki is a type of pottery produced in Hyogo Prefecture and has a long history of 1,000 years and has been produced continuously up to the present day. Tamba-yaki is produced by a kiln, and each kiln has its own unique style and texture. The molding method is based on "one-piece production," and no two Tamba potteries have the same pattern. Tamba-yaki is also characterized by the fact that it is fired with a natural glaze and no artificial glaze is used, making it the perfect vessel for appreciating the natural beauty of pottery.
Echizen Pottery

Echizen Pottery, produced in Echizen City, Fukui Prefecture, is one of the Six Ancient Kilns in Japan.
During the Edo period (1603-1867), the feudal lords encouraged the production of Echizen-yaki, and it spread as a regional specialty. Echizen Pottery, which comes in a wide variety of shapes, offers a wide range of items from daily necessities such as tea bowls and vases to gifts such as jugs and incense burners.
Shigaraki Pottery
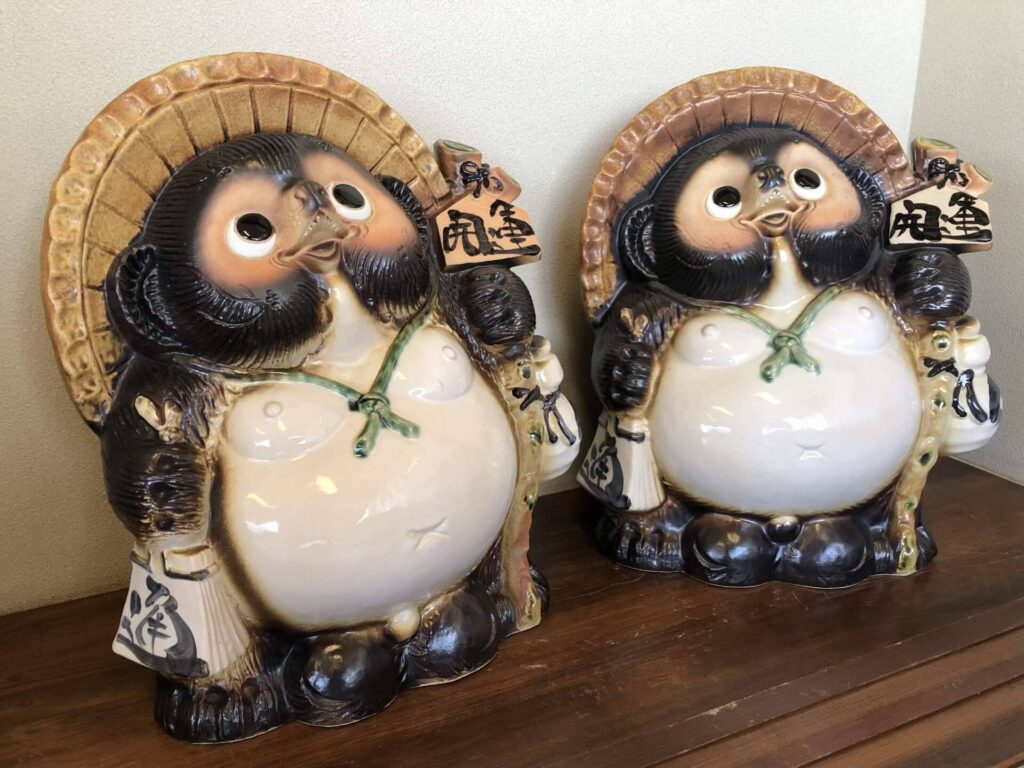
Shigaraki ware is a pottery produced in Shigaraki Town, Shiga Prefecture, and is popular among merchants as a lucky item for good fortune. Shigaraki ware has such a strong image that it is still used by business people to this day, and is often referred to as a Shigaraki ware with a raccoon dog figurine. Of course, in addition to raccoon figurines, Shigaraki ware also offers simple, austere, and tasteful teacups, teacups, and plates for daily use. It would be a good idea to have a Shigaraki ware in the family, both as a miscellaneous utensil for daily use and as a lucky item that brings happiness. In addition, tiles made of Shigaraki ware are actually used on the roof of the Japanese Diet building. It is amazing that Shigaraki ware protects not only raccoon figurines but also the country's politics!
How to Make Japanese Ceramics ?
Are you wondering how ceramics is actually made? You may have learned the characteristics of pottery and porcelain such as "the material" , "the firing temperature" , "the water absorption rate" but you may also be curious about the actual scene of making it.
In the following Youtube video, you can see the whole process from kneading porcelain clay, to molding using a potter's wheel, to detailed shaving to make a white porcelain tea bowl, and firing. We recommend you to watch the video because you will deepen your understanding of porcelain if you know how to make it!
Japanese Pottery and Porcelain is all beautiful, historic, and wonderful!
How was it? Japanese pottery and porcelain comes in a wide variety of types, all of which are beautiful and the techniques that have been passed down over time fascinate those who use them. When you think about the fact that the plates, bowls, vases, figurines, and other interior items we use in our daily lives are made possible by the elaborate techniques of craftsmen, you feel a sense of respect for them. I hope this article has been helpful in deepening your understanding of Japanese ceramics!